Equations [1], [2] and [3] can be combined to find terminal settling velocity corresponding to the droplet trajectory and the vessel dimensions:
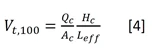
The minimum dispersed droplet sizes that would be fully separated at given flow rate can be found by substituting the terminal velocity equation [4] in appropriate settling law expression, such as Stoke’s Law:
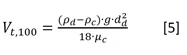
Where:
ρd – Density of dispersed phase.
ρc – Density of continuous phase.
g – Gravitational constant.
dd – Droplet size of dispersed phase.
µc – Dynamic viscosity of continuous phase.
Rearranging above equations, the separator dimensions can be expressed as a function of the operating and process conditions, which is known as the droplet-settling equation:
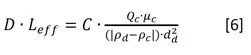
Where:
D – Separator diameter.
C – Dimensionless parameter, which is a function of gas-liquid interface level.
For an existing separator vessel, the dimensions (
D,
Leff) are known. Therefore, larger droplet size of the dispersed phase, due to the application of a low shear valve upstream of the separator, would enable higher production rates of the continuous phase. This is of course dependent on the downstream system being able to handle increased flow rates.
The low shear Typhoon System affects the feed stream by increasing, in comparison to standard valves, the average droplet sizes of the dispersed phase. The effect of Typhoon System on the droplet sizes can be graphically shown by plotting the droplet size distribution curves generated downstream a standard control valve and Typhoon System.
Figure 3. - Droplet size distribution curves for standard control valve and Typhoon System.
Figure 3 shows the results of experiments with a North Sea crude oil. The experiments are performed with a water/oil mixture with an oil concentration of approximately 2000ppm. The relatively low oil concentration is necessary to enable online droplet size measurements. For this reason, the average droplet size of the dispersed phase is also rather small. In actual field applications, due to much higher oil concentrations, the droplet sizes in the dispersed phase are normally around two orders higher to those from the lab experiments shown here. Real time measurements of the droplet distribution in the dispersed phase downstream of the choke valve are impossible to obtain, as the phase concentrations, mainly the oil and gas, are too high. Nevertheless, the indirect effect of a low shear Typhoon System is clearly observed in both field and lab tests through the reduction of the cumulative volume (ΔV OiW) of the dispersed oil content in produced water effluent. Field installations of a Typhoon System installed upstream the separator, resulted in a 45 to 60% reduction of the OiW content measured on the separator water outlet. Realistic lab tests showed a water quality improvement between 50 and 90%.
The droplet settling equation [6] can determine the smallest size of the dispersed droplets that would be completely separated, i.e. the separator droplet cut-off size -
dds. Using this droplet cut-off size together with the red droplet distribution curve from a standard choke valve (point “b” in Figure 3), enables one to calculate the dispersed oil volume in the produced water on the separator water outlet (point “a” in Figure 3). By replacing the standard choke valve with a Typhoon System, a higher droplet cut-off diameter -
dds (point “c” in Figure 3) can be used in the droplet settling equation for the same volume of dispersed oil carry over to the water phase. Improvement of the droplet size with the Typhoon System is shown by the blue droplet distribution curve.
As mentioned, for choke valve applications, it is not possible to directly measure the difference in droplet size due to the high fractions of oil, gas, and water present. A certain degree of coalescence can also be expected independent on the valve type that is used. Conservatively therefore an average droplet size increase of 10% to 15% is used in this paper to evaluate the result on the separator capacity.
To quantify the effect of the larger droplets when using a low shear Typhoon System, the droplet settling equation [6] can be used. For a given vessel, the left side of the equation is constant. Therefore, the increase in cut-off droplet diameter would allow less retention time required to obtain the same water quality, i.e. the production rate can be increased. A 10 to 15% increase in the droplet cut-off size due to use of Typhoon System, will enable 21 to 32% increase in production flow rate for a constant OiW content in the water outlet.
On the other hand, if the quality of the produced water is restricting production capacity, the improvement of the water quality when using the low shear Typhoon System, compared to a conventional choke valve, is also clear using Figure 3.
Using the same droplet cut-off sizer -
dds of the existing separation system together with the blue droplet distribution curve (point “d” in Figure 3) enables one the calculate the dispersed oil volume in the separator water outlet (point “e” in Figure 3). The difference in water quality compared to the standard choke valve can now be determined from Figure 3 (moving from point “a” to “e”).
More elaborate sizing models are available in the literature for the gravity separators, which may include coalescing effects in the feed pipe, flow distribution by separator’s inlet device, effect of separator internals, etc. The core of these more elaborate models, however, is still based on the droplet-settling theory. The effect of the use of low shear valves on the feed to the separator are therefore also clearly visible in these models.
TYPHOON SYSTEM APPLICABILITY TO GREEN FIELD PROJECTS
Including Typhoon System in the process plant design from the planning phase will help to optimize the separation system and prevent or significantly reduce formation of tight emulsions. Thorough evaluation of the capacity constraints can result in more compact separators necessary to satisfy the design parameters with regards to the separation efficiency required. Droplet-settling theory can be successfully applied for the sizing of the separator with regards to liquid carry over to gas phase, as well as oil and water carry over to the corresponding produced water and bulk oil streams.
For field conditions where gas-liquid ratio is expected to be low, it is fair to assume that the main three-phase separator capacity constraint would be the quality of the outlet liquid phases. Without available droplet size information, it is common to choose a recommended cut-off diameter size for separator sizing [6]. Recommendations can be found in SPE “Petroleum Engineering Handbook”. When using the same conservative assumption of the Typhoon System’s average droplet sizes increase range of 10-15% for the lower size range, the effect on the required separator size can be evaluated.
Equation [6] can be rewritten to evaluate the percentage reduction in the separator size that can be achieved by using low shear flow control technology:

Where:
dds – cut-off diameter generated by standard choke valve.
ddt – cut-off diameter generated by Typhoon System.
The 10 to 15% increase in
dd results in a 17 to 24% reduction of the effective separator volume required.
CONCLUSION
Reduction of shear forces acting on the fluids in the gathering system upstream of separation trains by utilization of low shear flow control technology, like the Typhoon System, minimizes droplet break-up and the formation of tight emulsions, thereby improving separation and increasing separation capacity.
Implementation of Typhoon System is a simple and efficient solution for debottlenecking the liquid capacity of a three-phase gravity separator. The Typhoon System retrofit does not require any modification to the separator itself. In most of the cases, Typhoon System can simply replace existing choke or control valves.
Furthermore, Typhoon System can be used to increase the separator efficiency instead of increasing its capacity. This is particularly useful when there are problems with reduced separator efficiency due to tight emulsions. Additional benefits could be a reduced requirement for separation enhancing production chemicals like demulsifiers and reduced heating of the liquids.